
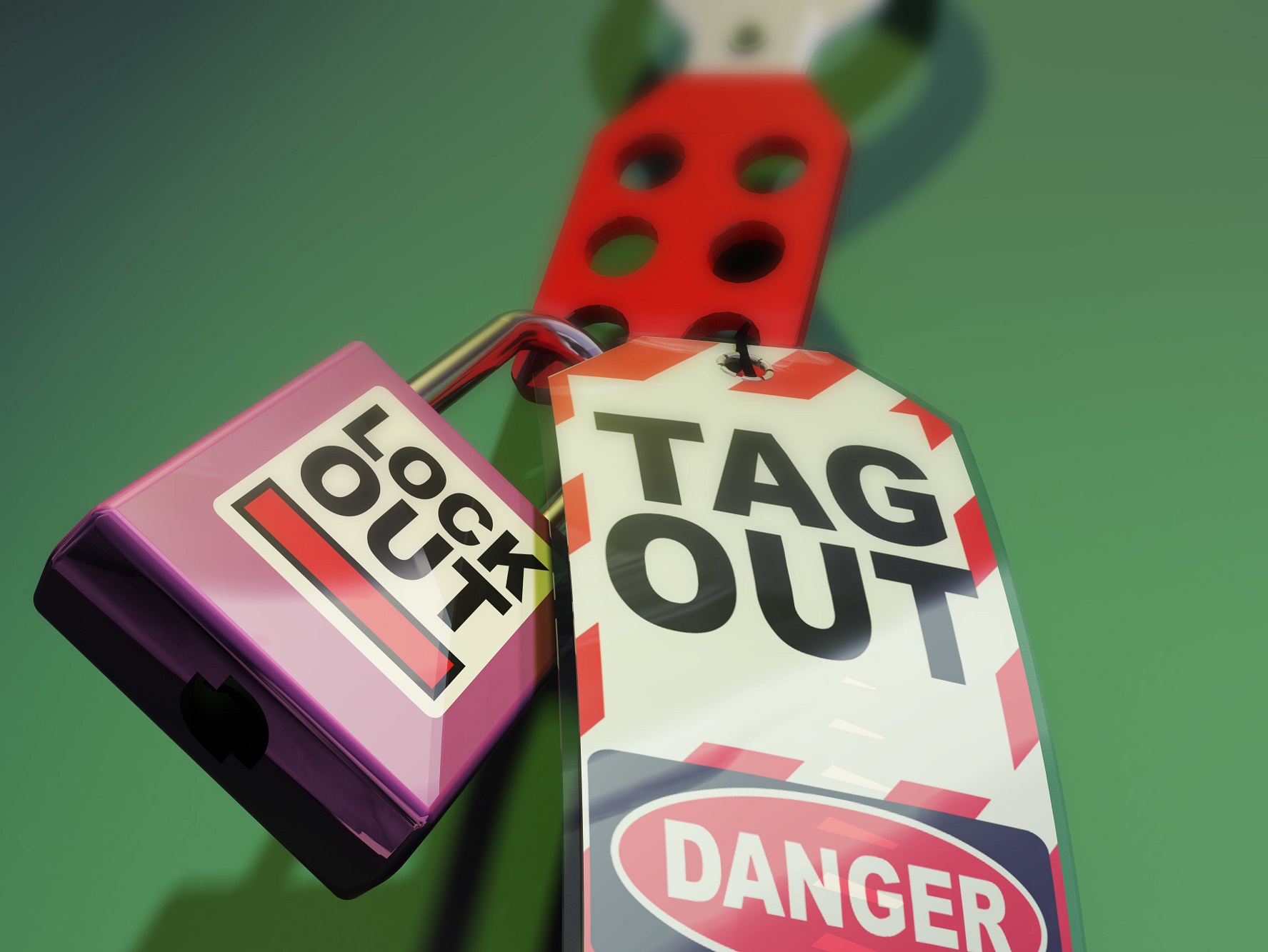
Consequently, there are several hundred written lockout/tagout procedures in place at these facilities. Although it is possible to develop generic procedures and supplement them with checklists and attachments, detailed standard operating procedures provide a higher level of safety. The use of these procedures is stressed in employee lockout/tagout training. There are also specific lockout/tagout procedures to isolate equipment during repair turns and during a major outage. Each operating department will have several written energy control procedures that may have common, but many times special measures, that must be taken to isolate equipment for servicing and repair. Question 1: In a large steel manufacturing facility there are numerous operating departments, e.g., blast furnace, electric furnace, coke ovens, hot mill, coating lines, machine shops, etc. Your questions, your suggested approaches, and our replies follow: This interpretation further clarifies previous interpretation letters on the periodic inspection requirements, and the policy will be incorporated into the forthcoming directive revision. 147, The Control of Hazardous Energy (Lockout/Tagout) - Inspection Procedures and Interpretative Guidance. OSHA is currently evaluating our directive on the lockout/tagout standard, OSHA Instruction STD 1-7.3. You had specific questions regarding the Control of hazardous energy (lockout/tagout). This letter constitutes OSHA's interpretation only of the requirements discussed and may not be applicable to any question(s) not delineated within your original correspondence.

We also appreciate the opportunity we had to discuss the concerns raised in this letter at our meeting on January 23, 2003.

Thank you for your Maletter to the Occupational Safety and Health Administration's (OSHA's) Directorate of Enforcement Programs (DEP).
